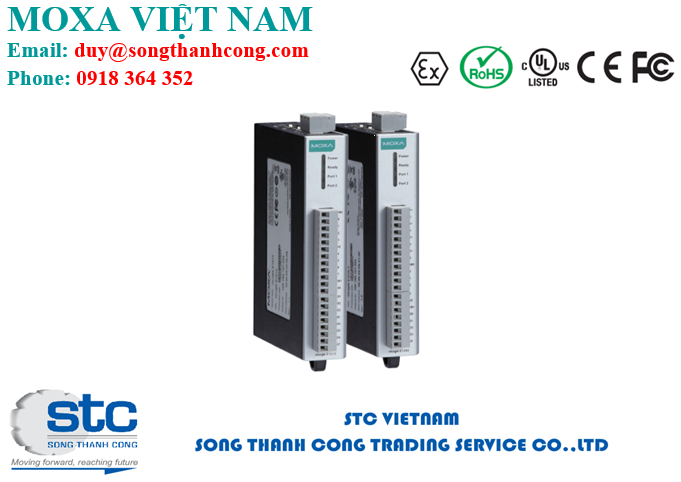
E1242 IoLogik Moxa Việt Nam
Xuất sứ: Taiwan
Nhà cung cấp: Moxa Viet Nam - STC Viet Nam
Hãng sản xuất: Moxa Inc
Ứng dụng sản phẩm: 1. Thiết bị điều khiển từ xa thông minh (Smart I/O) - Programmable Controller – Smart Remote I/O – Remote I/O – Automation Software
Giới thiệu Dòng thiết bị thu nhận tín hiệu.
E1242 IoLogik - Ethernet remote I/O with 2-port Ethernet switch, 4 DIs, 4 DIOs, 4 AIs
- User-definable Modbus/TCP Slave addressing
- Supports EtherNet/IP* adapter mode
- Supports RESTful API for IIOT applications
- 2-port Ethernet switch for daisy-chain topologies
- Save time and wiring cost with peer-to-peer communications
- Active communications with MX-AOPC UA Server
- Supports SNMPv1/v2c
- Easy mass deployment and configuration with ioSearch utility
- Friendly configuration via web browser
- Simplify I/O management with MXIO library on either a Windows or Linux platform
- Class I Division 2, ATEX Zone 2 certification
-
Wide operating temperature range: -40 to 75°C (-40 to 167°F)
*Requires online registration (available free of charge)
Introduction
I/O to IT/OT Protocol Conversion
The ioLogik E1200 does just what you need by supporting the most often-used protocols for retrieving I/O data. Most IT engineers use SNMP or RESTful API protocols, but IA engineers are more familiar with Operational Technologies (OT), such as Modbus and EtherNet/IP. Moxa's Smart I/O makes it possible for both IT and IA engineers to conveniently retrieve data from the same I/O device. The ioLogik E1200 series speaks six different protocols, including Modbus/TCP, EtherNet/IP, and Moxa AOPC for IA engineers, as well as SNMP, RESTful API, and Moxa MXIO library for IT engineers. The ioLogik E1200 retrieves I/O data and converts the data to any of these protocols at the same time, allowing you to get your applications connected easily and effortlessly. Learn more…
Daisy-chained Ethernet I/O Connection
A new daisy-chained Ethernet I/O concept is now available. The ioLogik E1210 industrial Ethernet remote I/O has two embedded Ethernet switch ports that allow information to flow to another local Ethernet device or connect to the next ioLogik in the daisy-chain.
Applications such as factory automation, security and surveillance systems, and tunnel monitoring, can make use of daisy-chained Ethernet for building multi-drop I/O networks over standard Ethernet cables. Many industrial automation users are familiar with the multi-drop configuration typically used in fieldbus applications. The daisy-chain function on the Ethernet remote I/O ioLogik E1210 not only increases the connection between machines and panels, but also lowers the cost of buying separate Ethernet switches, and at the same time reduces labor fees and cabling by a large percentage. For example, if a production facility contains 700 stations (20 points per station), the wiring cost reduction can reach 15% of the total implementation cost.
Saving Time and Wiring Costs with Peer-to-Peer Communications
In remote automation applications, the control room and sensors are often far removed, making wiring over long distances a constant challenge. With peer-to-peer networking, users may now map a pair of ioLogik E1200 series modules so that input values will be directly transferred to output channels, greatly simplifying the wiring process and reducing wiring costs.
User-definable Modbus/TCP Addressing for Painless Upgrading of Existing Systems
For Modbus devices that are controlled and detected by fixed addresses, users need to spend a vast amount of time researching and verifying the configurations. Users need to locate each device’s networking details like I/O channels, or vendor-defined addresses to enable the initial or start address of a SCADA system or PLC. The ioLogik E1200, with user-definable Modbus/TCP addressing, offers greater flexibility, and setup is easy. Instead of worrying about individual devices, users simply configure the function and address map to fit their needs.
ioLogik E1242 Specifications | |
• Inputs and Outputs | |
Digital Inputs | 4 channels |
Configurable DIOs (by jumper) | 4 channels |
Analog Inputs | 4 channels |
Isolation | 3k VDC or 2k Vrms |
• Digital Input | |
Sensor Type | Wet Contact (NPN or PNP), Dry Contact |
I/O Mode | DI or Event Counter |
Dry Contact | • On: short to GND • Off: open |
Wet Contact (DI to COM) | • On: 10 to 30 VDC • Off: 0 to 3 VDC |
Common Type | 4 points per COM |
Counter Frequency | 250 Hz |
Digital Filtering Time Interval | Software Configurable |
• Digital Output | |
Type | Sink |
I/O Mode | DO or Pulse Output |
Pulse Output Frequency | 500 Hz |
Over-Voltage Protection | 45 VDC |
Over-Current Protection | 2.6 A (4 channels @ 650 mA) |
Over-Temperature Shutdown | 175°C (typical), 150°C (min.) |
Current Rating | 200 mA per channel |
• Analog Input | |
Type | Differential input |
Resolution | 16 bits |
I/O Mode | Voltage / Current (jumper selectable) |
Input Range | 0 to 10 VDC, 0 to 20 mA, 4 to 20 mA, 4 to 20 mA (burnout detection) |
Accuracy | ±0.1% FSR @ 25°C ±0.3% FSR @ -10 and 60°C ±0.5% FSR @ -40 and 75°C |
Sampling Rate | • All channels: 12 samples/sec • Per channel: 3 samples/sec • Only one channel enabled: 12 samples/sec |
Input Impedance | 10 mega-ohms (min.) |
Built-in Resistor for Current Input | 120 ohms |
• Power Requirements | |
Input Voltage | 12 to 36 VDC |
Input Current | 139 mA @ 24 VDC |
• MTBF (mean time between failures) | |
Time | 502,210 hrs |
Standard | Telcordia SR332 |
• Common Specifications | |
• LAN | |
Ethernet | 2 switched 10/100 Mbps RJ45 ports |
Protection | 1.5 kV magnetic isolation |
Protocols | Modbus/TCP (Slave), EtherNet/IP*, SNMPv1/v2c, RESTful API, TCP/IP, UDP, DHCP, BOOTP, HTTP |
*Requires online registration at https://www.moxa.com/Event/DAC/2016/Smart_EIP_IO/index.htm (available free of charge) | |
• Physical Characteristics | |
Wiring | I/O cable max. 14 AWG |
Dimensions | 27.8 x 124 x 84 mm (1.09 x 4.88 x 3.31 in) |
Weight | Under 200 g (0.44 lb) |
Mounting | DIN rail or wall |
• Environmental Limits | |
Operating Temperature | Standard Models: -10 to 60°C (14 to 140°F) Wide Temp. Models: -40 to 75°C (-40 to 167°F) |
Storage Temperature | -40 to 85°C (-40 to 185°F) |
Ambient Relative Humidity | 5 to 95% (non-condensing) |
Shock | IEC 60068-2-27 |
Vibration | IEC 60068-2-6 |
Altitude | Up to 2000 m |
Note | Please contact Moxa if you require products guaranteed to function properly at higher altitudes. |
• Standards and Certifications | |
Safety | UL 508 |
EMC | EN 55032, EN 55024, EN 61000-3-2/3-3, EN 61000-6-2/6-4 |
EMI | CISPR 32, FCC Part 15B Class A |
EMS | IEC 61000-4-2 ESD: Contact: 4 kV; Air: 8 kV IEC 61000-4-3 RS: 80 MHz to 1 GHz: 3 V/m IEC 61000-4-4 EFT: Power: 2 kV; Signal: 1 kV IEC 61000-4-5 Surge: Power: 2 kV; Signal: 1 kV IEC 61000-4-6 CS: 10 V IEC 61000-4-8 |
Hazardous Location | Class 1 Division 2, ATEX Zone 2 |
Green Product | RoHS, CRoHS, WEEE |
Note | Please check Moxa’s website for the most up-to-date certification status. |
• Warranty | |
Warranty Period | 5 years |
Details | See www.moxa.com/warranty |
Note | Because of the limited lifetime of power relays, products that use this component are covered by a 2-year warranty. |